
|
|
Production
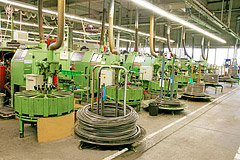 |
Our cold forming plant based in Ense, Germany operates 36 cold forming presses, ranging from 2 die up to 6 stage machines that provide up to 120 tonnes of pressure force allowing us to form wire from 3mm – 16mm with a level of precision which in the past could often only be reliably achieved with turned parts.
Our 6 stage machines are able to produce very complicated geometries and for some parts we are also able to use segmented dies for extra efficiencies. We can produce parts ranging from 4mm to 100mm long and head diameters up to 30mm in one pass.
The benefits of cold extrusion are high dimensional accuracy, good surface quality, high reproducibility thanks to keyed tools, an uninterrupted grain orientation and an economically optimal procedure for mass-produced items.
With the capacity to produce up to 75 million parts per month we are the choice for high volume cold formed parts.
Customers requiring on site audits of our processes are most welcomed, our extensive technical and production departments in Ense will be happy to assist you with any requirements.
Our UK based operation produces hot forged and bar turned parts for quick turnaround urgent and small to medium batch requirements.
We can manufacture hot forged parts from 5mm to 16mm diameters and 150mm in length. Our Bar Turned service can manufacture parts from 5mm to 150mm diameter and up to 1 metre in length. |
|
|
|
|
Secondary Operations
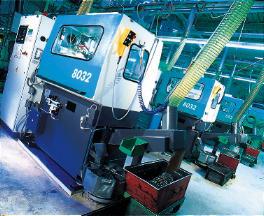 |
In addition to our modern pressing plant in Ense, cutting and mechanical operations can be carried out in downstream work processes. Our CNC-controlled finishing machines are designed for complex turning geometries such as knurling, thread moulding, rolling or drilling. We also work together with certified service providers to have various processing work carried out such as special coatings, tempering, hardening, thread locking and plastic coatings. |
|
|
|
|
Materials
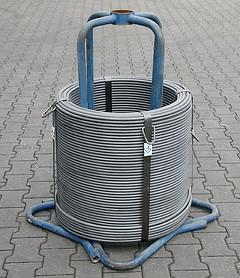 |
Materials supplied include alloys (B7, B7M, L7, L7M etc.), Stainless Steel (304, 316 etc.), Super Duplex, Grade 660A & B, Inconel, Waspalloy, Hastelloy, MP159, Monel, Nimonic, Aluminium, Titanium and many more. |
|
|
|
|
Surface Technology
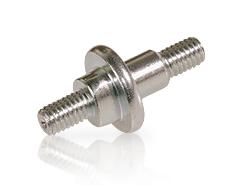 |
Our computer controlled surface treatment plant is capable of producing high quality surface finishes to 20 microns. Quality is guaranteed by x-ray inspection stations networked to the CAQ system. |
|
|
In-House Tooling
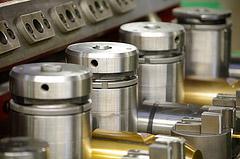 |
Our high-performance tool manufacture & machine construction facility in Ense permits the direct translation of a customer requirement into series production. Cutting-edge manufacturing technology enables us to produce high quality tools and machinery with long service lives. |
|
|
|
|
Development
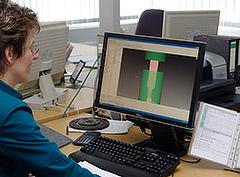 |
Customer designs are translated by our development department into tool concepts which are created with our modern CAD system. Here close co-operation with our customers and technologically flawless solution suggestions are the cornerstones of our success.
The use of finite element simulations reduces development times, minimises manufacturing costs, increases innovation and identifies and eliminates potential fault parameters. |
|
|
|
|
Certification
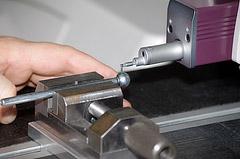 |
All parts supplied are fully certified to customers’ standard requirements, (including PPAP Level 111 to the Automotive Industry) and, with the aid of local UKAS & NAMAS approved testing companies, any extra requirements can be covered (i.e. Charpy, Tensile & 3.1.C. Witness Testing, NDE etc.).
We are ISO 9001:2008 & TS 16949 approved, and as such maintain a high level of control on quality, delivery and traceability. |
|